DIY liquid mold is a new type of silicone molds, various kinds of animals, flowers, fruits and crafts, etc., each can be done, do it all is exquisite, DIY liquid mold is the main material is liquid silicone.
Liquid silicone is a non-toxic, heat-resistant, highly recoverable flexible thermosetting transparent material of organic silicone, its sulfuric behavior is mainly manifested in low viscosity, rapid curing, shear thinning and higher coefficient of thermal expansion. Two-component high transparent, high strength, high tear resistance liquid silicone rubber suitable for injection molding process.
Liquid silicone rubber includes liquid silicone rubber, 0 degree liquid silicone rubber, zero degree liquid silicone rubber, 5 degree liquid silicone rubber, 10 degree liquid silicone rubber, 15 degree liquid silicone rubber, 20 degree liquid silicone rubber, 25 degree liquid silicone rubber, 30 degree liquid silicone rubber, 40 degree liquid silicone rubber, 50 degree liquid silicone rubber, 60 degree liquid silicone rubber, 80 degree liquid silicone rubber, which are various hardnesses of liquid silicone rubber in the market silicone rubber. When we produce DIY liquid molds, we can choose different hardnesses of liquid rubber according to our needs of producing molds.
The production process of DIY liquid molds:
Design DIY products
Draw 3D prototypes
Confirmation prototypes
Prototype drawings
Output samples
Mass production
There are often problems encountered when manufacturing liquid silicone molds, so what are some of these matters that we should be aware of? In general, the structure of liquid silicone molds is similar to that of thermoplastics, but there are many significant differences. The viscosity of liquid silicone is generally lower, so the filling time is shorter, even at very low injection pressures. To avoid air trapping, a good venting device must be present in the mold.
In addition, liquid silicones do not shrink in the mold as thermoplastic compounds do. They tend to undergo thermal expansion and do not shrink slightly as expected so that their product does not remain on the convex side of the mold as expected. It gets stuck within the larger surface area of the mold cavity.
Precautions for manufacturing liquid silicone molds.
1. Shrinkage
Although liquid silica does not shrink in the mold, it will typically shrink after demolding and cooling by 2.5 to 3. The exact degree of shrinkage depends to some extent on the formulation of the compound. However, from a mold perspective, shrinkage can be affected by several factors, including the mold temperature, the temperature at which the compound is demolded, the pressure within the cavity, and subsequent compression.
The location of the injection point is also worth considering, as shrinkage in the direction of compound flow is usually greater than shrinkage in the direction perpendicular to the compound. The shape of the product size also has an effect on its shrinkage, with thicker products generally shrinking less.
2. Parting line
The first step in the design of a silicone rubber injection mold is to determine the location of the parting line. Venting is mainly achieved through a groove located on the parting line, which must be located in the area where the injected rubber will eventually reach, thus avoiding the formation of air bubbles and reducing the loss of strength in the bonded joint.
Due to the low viscosity of the liquid silicone, the parting line must be accurate to avoid spillage. Even so, parting lines can often be seen on the final product. Liquid silicone molds are influenced by the geometry of the product and the location of the parting line. A slightly chamfered product design helps ensure that the product has a consistent affinity to the desired other half of the cavity.
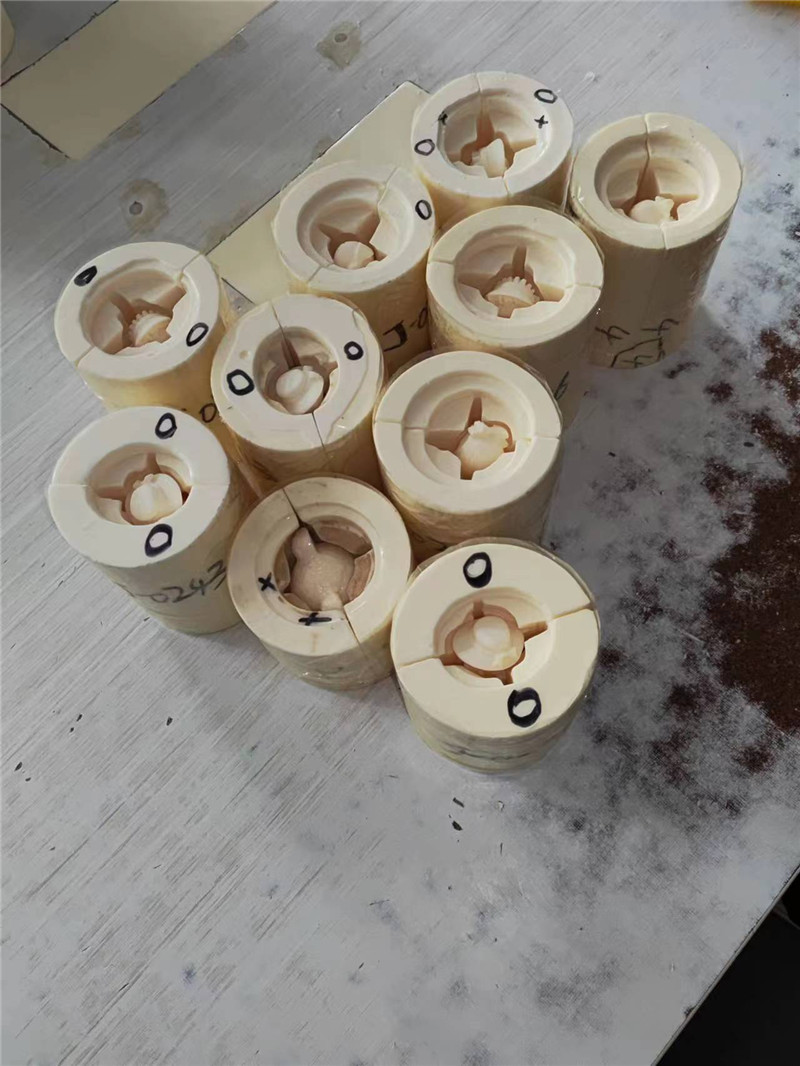
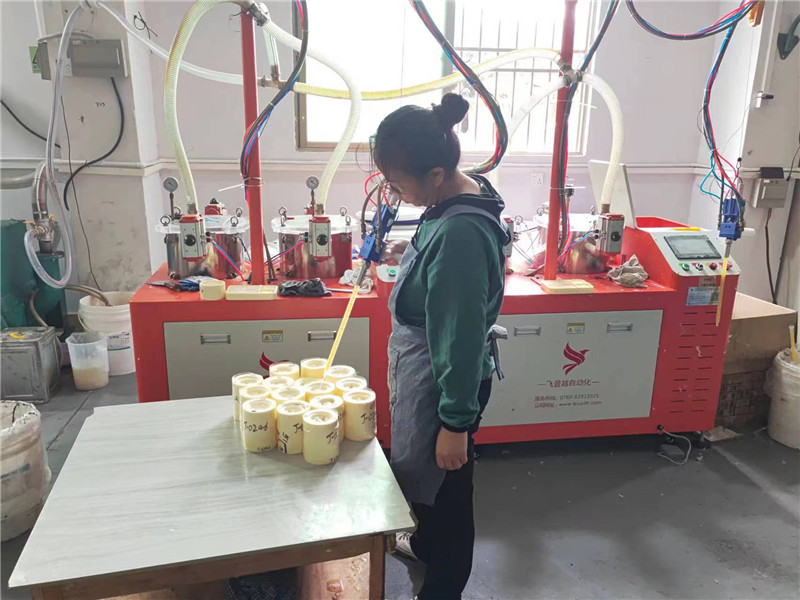
Post time: Feb-24-2023